Adventures have a way of interlocking, after we sold the 57 in 74, I traded a dude a truck rear end for a VW dune buggy, typical for that generation, a beetle pan and roll bars. I was always intrigued by the VW torsion bar front end. Every VW I have ever been involved with had gas delivery issues, similar to the phenom that I never been told I have high blood pressure without a nurse involved! This animal was no different, just about time you were ready to hang on, it shut off. I hunted all over for a carb. The fuel system was simple, the factory fuel pumps were challenging at best, like a Briggs choke until you get enough suction, by then the battery is dead. So, I found a $15 electric fuel pump, $4 toggle switch, threw the steal factory lines in the trash, bought an aluminum beer keg, tapped a 1/4 pipe in the tap hole, and run rubber lines to the carb. The carb looked simple, but as any first time take a part mechanic, I took it apart as random as a spring day, cleaned it and put it right back on the car. Well, that was an adventure, I might as well of tossed it in the river. Rumor was Russel Norman could fix the carb, I explained the tear down and Russel changed my carb experience into an assembly lesson. He explained factory carbs that don’t run are normally dirty, yee-haws are quick to adjust not clean, there are only a few wear issues in carbs. VW’s had a brass float and in some crazy situations they wear a whole in them, take apart mechanics fly in and disassemble without verifying the adjustments losing the factory settings. A VW rebuild kit has a procedure of assembly sheet; each adjustment is documented. Russel had the assembly sheet and within a few minutes the dune buggy was running. Russel explained that he was told in a VW training deal never doubt the build sheets, and always remember that the folks that assemble cars are not mechanics, they are just bolting together assemblies. Lesson learned. The VW was a ton of fun, adrenaline junkies love playing with anything that takes their breath, but after driving the 57 the VW was like a toy. Russel called and asked if I would trade the VW for a hot rod, I was never attached to any possession, so I was like sure. A couple days later a dad of a kid I went to school with called, said he bought a hot rod/ dune buggy from a guy to teach his 12-year-old twins to drive. He explained it cranked but wouldn’t stay running, he bought it from a pipefitter dude on his job sight but after getting it home was pretty sure it was over their ability to drive. The VW was 53hp with big old steel wheels and muddier tires, 40 mph at best. I got there and the hot rod was just that, today we would call it a Rat Rod. The picture below is very similar to my build.
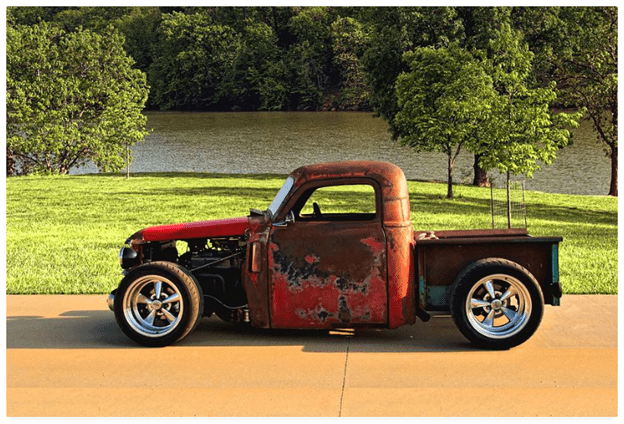
The chassis was a 66 Galaxy both side rails cut out, the wheelbase was shortened to 84 inches, 9 in Ford rear end, 4:00 gear Detroit locker, 390 cubic inch 402 hp/ 427 torque, factory Holley 4bbl.and C4 automatic transmission, the body was a channeled 1950 Chevy 5 Window truck, the bed was shortened to 2ft with tailgate. The interior was stock with 2 mustang seats and a mustang floor shift. This was not a toy, we traded right there. After we got it to the shop, I studied the car and the fabrication, went through the all the systems, the running and stopping issue appeared to be fuel centered, at the end of chasing fuel, we realized that the OEM wiring system from the car was trashed, the ignition system was hotwired, sending 12 volts directly to the coil, Ford uses a resistor and cold start rely, using the stock wiring loom diagram, we recreated a simple wiring loom for the ignition. I had started the engine 100 times or more, but it would only run a few minutes at a time. After the wiring issue was corrected the engine ran strong but would run hot within minutes pushing water out the overflow. I checked the thermostat, it was new, radiator was in great shape, hoses were new, Don’s bother Danny came in looked at it and said it’s the Chevy radiator cap we all laughed and continued, I was getting ready to start it up and realized that the radiator cap was a 4lb cap the Fords all used 20 lb. caps changed it, fix it! The next adventure was the driveline, we had the stock driveshaft, but the drive shaft place refused to take out 32 inches, after making a field trip to the drive shaft store our “if they can we can” kicked in, the builders had cut the original shaft in half, we cut, ground weld off, dressed the end so it would side in the cut tube, matched the witness lines and welded. We got ready to make a run, drove around shifted up, shifted down, tested the brakes, took her north on 7th to the ball field, no vibrations, around the corner back on Macclenny Ave into Cal’s parking lot. I told Don time to hammer down, backed up to the wall, launched on the concrete, out on Macclenny Ave hammer down and BAM!!!!!! The driveshaft went spinning like a top down Macclenny Ave. We realized after the driveshaft ripped out that we welded on the witness lines, but it was phased 90* out. As Wally “Fatman” Ferry would say “that screw up just became valuable knowledge”. A local Ford tech put his eyes on the issue told me to get a ¾ ton Ford Pickup drive shaft. Found one, cut the rear yoke end off, took it to a local machine shop to dress the excess tube off the yoke. Then using a Ford OEM standard procedure manual I timed the yokes to the exact position to weld, heated the tube to 200* put the yoke that had been in freezer for an hour, slid together tapping slightly, set the assembly in a homemade angle iron fixture, using a dial indicator checked the run out, then warmed the yoke/ tube weld area to 400 degrees and MIG welded. After reinstalling new Moog universal joints this adventure cost about $200 in 1976 money. So, we piddled around with the driveline after the new driveshaft was installed to be sure the pinion angle and engine angle were correct, as you can imagine they were not in line so to correct the angles we had to redrill the stock Ford trailing arms to adjust the pinion angle. This is an example of knowing what the results needed to be and you fix it. The next drive happened early on a Sunday morning, hammer down, donuts, burnouts, 180’s and brake slides, I was in the middle of a series of donuts and my dad drove up. My dad and I had a history of discussing our differences of opinion in loud debates, this one started with the “oh hell no, it’s 7am on Sunday morning in the middle of town! My response was church don’t start it 9:45! His next statement stuck “sell it, the one thing I don’t need is raising a vegetable stuck in a hospital bed for being stupid! Until then park it put the keys in the office! I told him that was the plan, got to raise money to build a new race car! (Another sore spot in our relationship at the time) after a discussion of image, being professionals, and working 24/7, to having no say in business decisions we went our separate ways for the day. As I was parking the 50 hot rod a local kid pulled up, and asked are you selling that, I answered I guess so, 1st $4000 has it, he said be here tomorrow. When I got to the shop at 8am he was there, we loaded it up and sent him on his way. As I mention in a number of my adventures, after the first race with the 56, stuff was only worth the sum of the parts not destroyed in the crash, but everything is for sale. I have always had the ability to turn something over to fund the next adventure.