When we left for Talladega on Wednesday, we never realized the chain of events that would affect our lives for months to come. I never attended being invited to the biggest fence building party at a racetrack. Daylight was running out, Davey was leading, we were scrambling to load everything, as Davey made it to victory lane, we were on the road to NC after a 15-hour May Day at the track. Carlise made the call to drive to South of Atlanta to eat, as we stopped, I called Darlene to let her know we were riding safe, she said Jesse called and decided to stay the night with the big truck, all was good but really tired. Four hours later we rolled into Kannapolis, our instructions were to meet at 12:00pm to unload the truck. As we got to the shop, we were informed Jesse had been in a wreck, he had two volunteers with him, Jesse was in the hospital, the boys were safe and released, the truck was destroyed. The star athlete from Va Tech that fell asleep died in the wreck as he crossed the meridian launched off the concrete barrier hitting Jesse windshield high flipping the big truck over. The wreck rocked the industry as much as the Allison wreck. We pushed the envelope many times in the early days, 12–16-hour days on Raceday, then drove home because it saved money. I remember driving to Michigan on Saturday, 12 hours from Kannapolis, asleep at midnight, at the track at 5am, race till 5 pm, load head home getting to shop a 5am. 24 hours of wide open! This didn’t change until we started flying in 1990. Jesse’s wreck changed the plans for the summer. Dad had joined the Curb team; his focus as well as Carlise’s was the trailer fiasco, the Johnson boys focus was on the engine shop, I made a deal with Corey Fillip and the owner of the Landis shop to take up the $400 per month lease. The Motorsports Fabrication adventure was starting. I started chasing cars to build and getting tools. Dave and Don Roberts were building Don a Daytona Dash car we split the rent, and toying with hot rods. My first project was hanging a body on a Concord Car. The collective was switching from dirt to asphalt. As I was tying up loose ends, a dude that was a car restoration guru showed up, he had several obsolete NASCAR racers that needed love. Alex Beam was a racing historian, his business deals needed close watching, he chased dollars in random ways. His interpretation of profit taught me a lot, we were loosely in business together until 1997. Our business relationship started with a contract to restore, paint, and assemble four original race cars back to as close as Alex would spend.
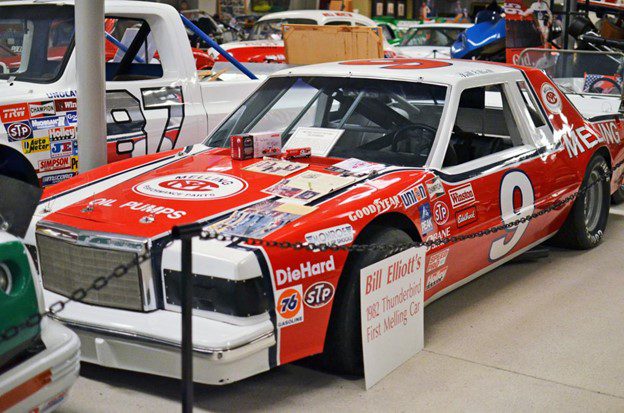
They had original paint, banged up, cracked Bondo, missing parts. The first we restored was a 1980 Bill Elliott Road Course car used in the Six Pack movie, still had movie paint/ 49 on the side.
The next restoration was a 1981 Bud Moore Wrangler car, left quarter fill hole was cut out, fuel cell can and reinforcement ripped out rear bumper ripped off. Then a Blue Max Alugard car, every panel was crashed, and a DW 11 Budweiser Car, crashed front clip. It was a start. The first Beam contract was $20,000, $5,000 per car, $,5000 up front, $3,750 every time a finish piece rolled out the door. The first two were a breeze, body and paint very little fab, the Blue Max car was what Harold Elliott, called a rookie throw away, and about the only car that survived Tim Richmond. The truth was it was a workhorse named Sampson, Tim used it up and won 2 races with it, Rusty equaled the feet, this car had damage all around, with Blue Max going to the 1988 Pontiac, the car a 1987 2+2 car, just didn’t have any value was stripped and stacked out back.
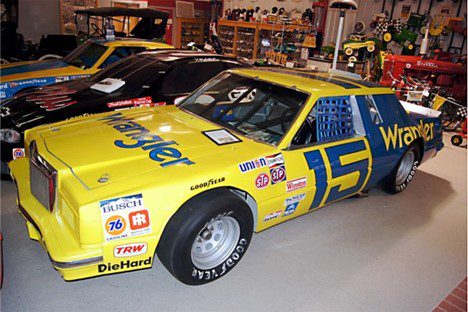
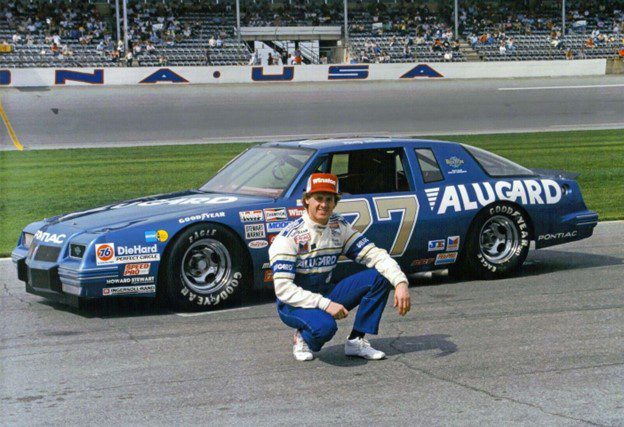
The DW Budweiser car Alex Beam purchased from Tim Brewer@ Jr Johnson Associates was the toughest to repair, front and rear clips were both bent, patched and bodied back. The crazy thing was the interest in the car. Within days of getting the car, 3 or 4 front running crew chiefs showed up to look at the car. After all the interest, I was paid by GM Tech Team to map and document the Banjo rear steer car Darrel Waltrip won 13 races with. The car won 7 in 1984, 3 in 1985, and 3 in 1986. After mapping the front end, we passed the information on to GM to distribute to the GM teams. After mapping the front end, we documented that the car had .100 bump out right,. 200 bump out left, per inch of travel, Akerman gain per 10 degrees of steering was .200. Rear steers also can lead the front suspension, the 11-car wheelbase was 111” on the left ,109.5” on the right. The front clip was mounted 1 inch off center, after reviewing the shock travel notes from various competitions, the car on entry had almost .500 toe out in the left, .250 toe out in the right. ¾ of an inch shock travel total/ 10* steering to the left. Now scrub kills HP but it complements drive feel, in fact the 11-car turned in almost on its own, tire wear was consistent. How did DW win with that much parasitic scrub? Jr Johnson’s engine room through 1986 was consistently 50 to 75 HP better than most of the other cars. Our only conclusion was DW the driver exerted less energy throughout the race and was fresher to race at the end. The teams that had cars with the old school challenged geometry similar to DW’s with 50 less HP were back markers. Rear steer and front steer teams with corrected geometry could have 50 less HP could race equal to or slightly slower (Blue Max, Hendricks, Baker/ Schiff, Curb). Long run DW’s 11 stayed consistently 3 tenths better in a fuel run. Teams down 50 HP with the same basic setup and frontend geometry were lapped within the first fuel run. Earnhardt was a stronger driver, but Childress engines were conservative at best (20 to 30 hp off), they were fishing for championships with better bait (Earnhardt). On any given day the 3-car crew could roll back the parasitic scrub, tune the steering geometry, back the caster out, tune the lead in the front end and let Dale be Dale, they could beat DW. DW’s domination days were over, Jr’s days were numbered with the rear steer cars.
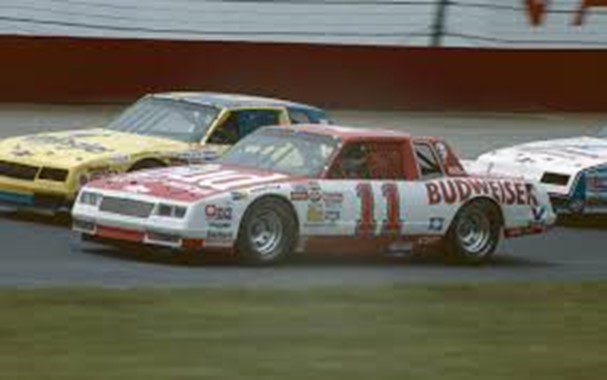
In late 1987 I got the chance to hang a few 1988 bodies for Pontiac teams mostly at their shops. Bahari had recruited Mike Beam for crew chief, this meant the band was back together, “not!” Dick Bahre had a collection of junk, and every piece of equipment in the shop was homemade or wore out. I was convinced to battle this recurring issue, I needed to upfit a shop for fabrication that included sheet metal fabrication, not just bodywork, we needed a sheet metal brake, shear, slip roller, bead roller, English wheel, belt sanders, vertical and horizontal saw. I reached out to a leasing company, with crazy interest rates, with a payment plan, $800 per month, for 24 months. The project was to build 10 bodies for underfunded teams, Pontiac paid half, teams paid half. With a prayer, a promise, a payment, two contract labor helpers and a 5,000 sq ft leased shop the adventure started. Within six months I paid the equipment lease off, as the projects matured, we expanded our capabilities with talent and equipment.